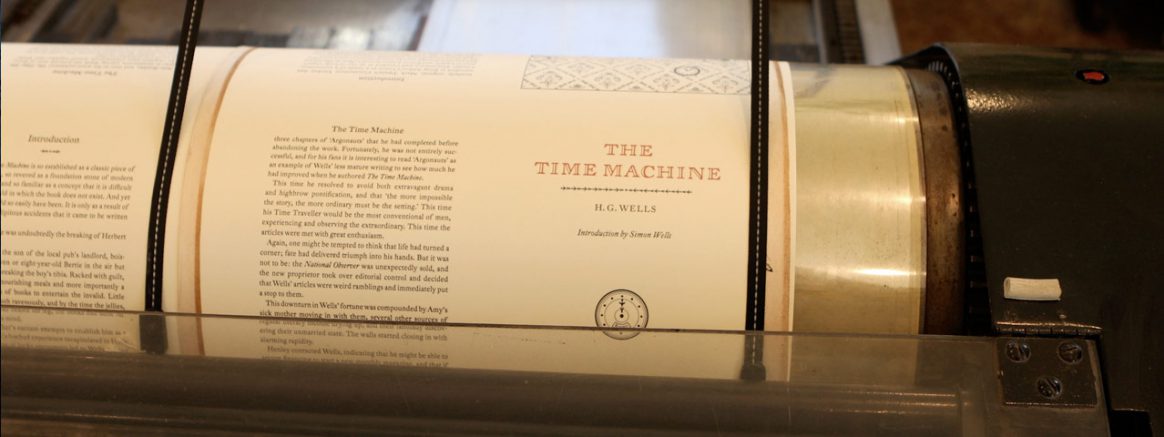
Like so many things, printing is easy, but printing well is hard. The concept is simple enough. If a rubber roller coated with thick and tacky ink is rolled over a raised surface, the ink will transfer only to those high areas. Then, if paper is pressed into contact with the inked surface, the ink will transfer to the paper. This is essentially what the historic craft of letterpress printing is all about.
The plates are made of photo polymer. They are made using a photographic process that allows images and text to be transferred to a light sensitive plate. The non-image areas are safely dissolved away in water and a perfect dimensional reverse image of the final print is revealed. Polymer serves as a bridge that allows the scanned drawings of artists and the digital layouts of designers to be printed on these old machines.
The press itself is rather unusual. Actually all letterpress equipment has become a rarity as the process began to fall out of mainstream commercial viability many years ago in favor of faster and cheaper, though not so elegant, printing methods. The Vandercook Universal IV press used to print The Time Machine is one of the latest I own, built in the late 1960s. Indeed, even when it was new, this press must have seemed a bit old-fashioned as by the end of the 1970s Vandercook would no longer be making presses and letterpress equipment was being scrapped on a vast scale.
The Universal IV is particularly desirable because of its size. It is double the size of most of the presses Vandercook made, and one of only four of this model known to exist. Like most of my equipment, it didn’t work when I got it. It had been neglected and dismantled down to nearly every last screw and bolt. The previous owner never used it and didn’t know if it was all there or not. I bought 3000 pounds of scrap metal consisting of a giant solid steel base and a plethora of old collapsing cardboard boxes of parts. Turns out nearly all of it was there. I put it back together myself; it wasn’t easy. It is not a fast press, or a production press, I have other presses for that, but it prints beautifully.
Every sheet is handled many times. Eight pages are printed at once, and the sheet must be fed by hand, and removed from the press by hand. The other side of the sheet will go through the same process. The text alone will require 24 separate runs of the press. Great care must be taken to line everything up. The printer must shim and make small adjustments to each plate to make up for slight differences in the way they print. Differences in the amount of surface area to be printed means each page behaves a little differently. It is a long process.
If you listen carefully to the paper running through the press you can hear that soft sound of the ink and paper becoming one.—Robert LoMascolo, Letterpress Printer
There is nothing to tell the printer when to add ink, the printer needs to add it as he judges. The prints are all minutely different. The weather will change the way the press runs. The ink knows when it is hot or cold. The paper knows if is humid or dry. It is the printer’s job to try to keep the prints consistent, but they are all individuals filled with life. The type bites into the paper, not a lot, but it is unmistakably there. If you listen carefully to the paper running through the press you can hear that soft sound of the ink and paper becoming one, like sticky bare feet scampering along a wooden floor. You can feel it, the prints are tactile. I am always struck by how “real” letterpress is. Real in the way it feels and the smell of the paper and ink. Real in an honest sort of way. Type on a computer screen, despite its seeming perfection is little more to me than anemic shadows of letters floating in space. How much more real are physical, dimensional letters forced into the very fibers of good paper? They have presence…they are real.
The black ink was made by the Royal Dutch Printing Ink Factories of Holland, though it isn’t letterpress ink. Letterpress inks like everything else haven’t been made in a long time. It works well though. The red ink on the title page must be printed in its own pass through the press. Colors are mixed by eye. A bit of orange ink mixed with scarlet red makes a vermillion that isn’t found in a swatch book. It is not the easy way of doing things, but the product achieved can not be matched nor surpassed with any modern process.
— Robert LoMascolo,
Letterpress Printer
October 2019
David Cowart
This is amazing. Thank you for sharing wit us.
David
Peter Edward Cozzens
Very instructive and nicely produced video. Thank you!
Rui
Beautiful ! thanks for sharing
Dana Jean
Am I the only nerd who almost bawled watching this?
Art. Craftsmanship. Mad skills. I love that this is still happening. We are losing ourselves to instant gratification. Watching this video was like waiting for Christmas morning.
Antici….pation!